Having been in the armor business for a number of years starting right after 9/11, we found that carbon fiber was two brittle. Armor consists of multiple layer constructions where each layer plays a specific role in defeating the threat.
The role composite armor plays in that sandwich could be likened to a catcher’s mitt. Armor generally consist of a strike face, which is something like AR500 steel, then has a ceramic plate behind it, and the composite materials are the last layer.
Depending on the threat, the projectile passes through the steel, which deforms it giving it a larger footprint and slows it down, the ceramic breaks the projectile into smaller pieces called spall, and the composite referred to as a spall liner catches the spall.
I’ve attached an image showing a .30-06 caliber armor piercing incendiary round lodged in a consolidation of Spectra and Polystrand. Polystrand is S2-Glass that is laminated in 0° / 90° cross bands, with each corresponding layer being in that same orientation.
The composite portion of this armor consolidation was about a .250” thick. The other two layers were .125” thick each and consisted of AR500 and ceramic. This armor layup weighed 7lbs per sqft, and stopped the round within 15’ of target, traveling at 2800 ft per sec.
This particular armor was for a riverine gunboat, which I've attached a picture of.
I’ve also attached a picture showing a consolidation of pure Polystrand used in the .500” thick AR500 floor of armored tactical vehicles. This is the spall liner that is combined with the steel, which is used to defeat mines and IEDs. You can see the thickness in relationship to the dime.
In all the testing we did, we never found carbon fiber to be a suitable material for armor, but Kevlar is used a lot as it has good flexural strength.
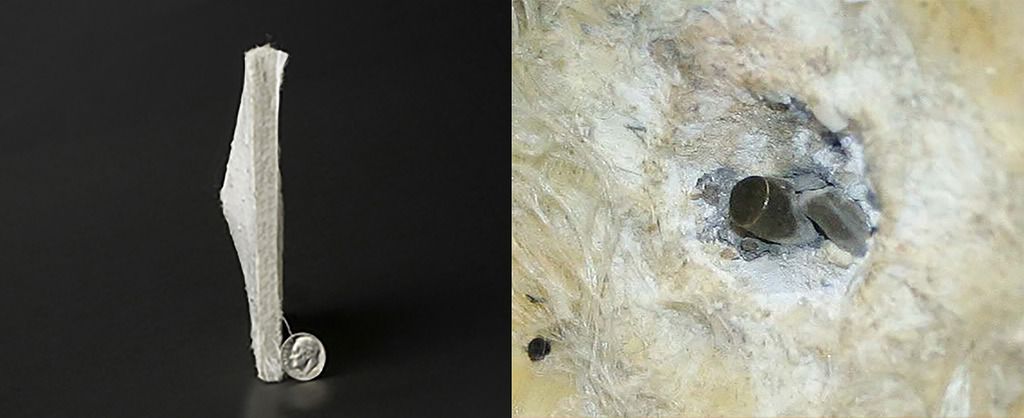
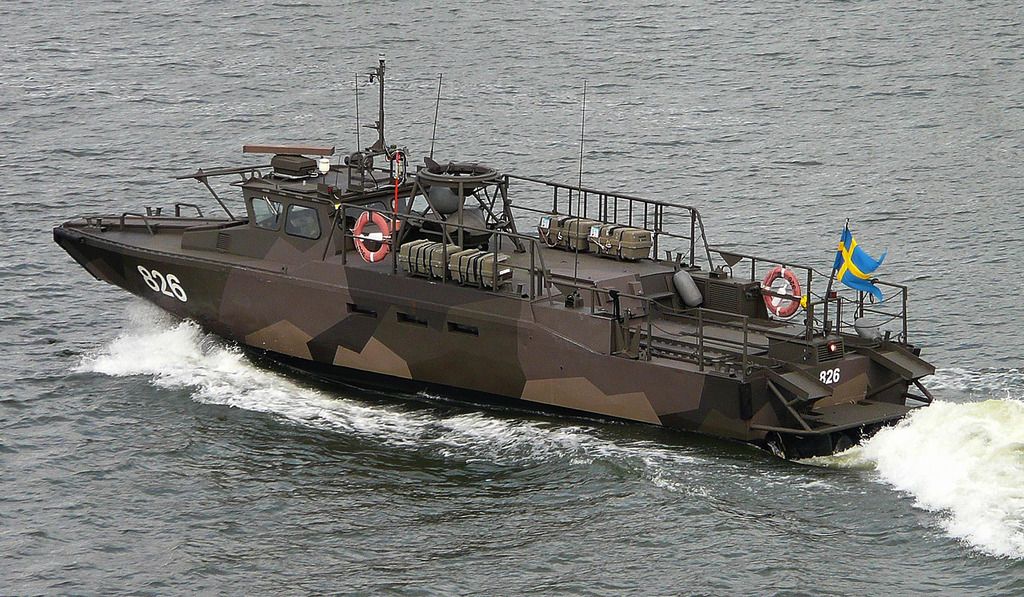
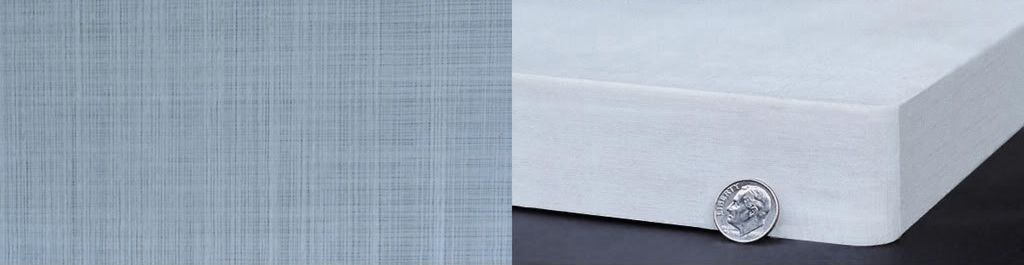