OK…so I think I’m going to approach my questions differently as I’m not sure I’m hearing what I was hoping for, so I’ll do this in a question format with pictures.
In the following picture I’ve shown arrows where there are exposed edges that are seen, so this top edge needs to be cosmetically perfect both visually and dimensionally on the lower hand guard.
In these next two pictures of the lower hand guard you can see where there are critical surfaces on the front that need to be formed dimensionally to within +/- .030”. There are similar critical surfaces on the back end, as well on the inside on both ends.
In the next three CAD renderings you can see arrows pointing to an upside down isometric view of the upper hand guard where there are also similar critical surfaces on the back and front end, as well as inside.
I’m about half way through making the plugs for these two parts and my next step is doing the split molds. I will be using an autoclave that has heat, vacuum and pressure, which you can see pictures of at: http://www.talkcomposites.com/21718/I%E2%80%99m-the-new-guy-from-Oregon-USA
Question 1. Are these molds needing to be two halves that split down the middle, with molds on both ends, and a male mandrel coming in from the top, where all 5 sections are bolted together to form a completely closed mold?
Question 2. Knowing that I want the outer visible surfaces to be cosmetically perfect with the orientation of the twill weave pattern, is it safe to assume that this needs to be all pre preg, or are there other options that includes infusion.
Question 3. If they are all pre preg; how do I insure that I get the correct number of layers in the areas where the inside is built up, or is that strictly trial and error?
I’m using rapid prototypes on the plugs, as I find they are dimensionally more stable in terms of twist, bow and warping than production injection molded parts. And they are of a material that lends itself to making changes using body putty and accept gel coat nicely. I’m also making these where the vents in the sides will be CNC machined in afterward and then be clear coated on the finished production parts.
I sincerely appreciate your input here, as I have no real clue what I’m doing, other than what I’ve seen watching videos!

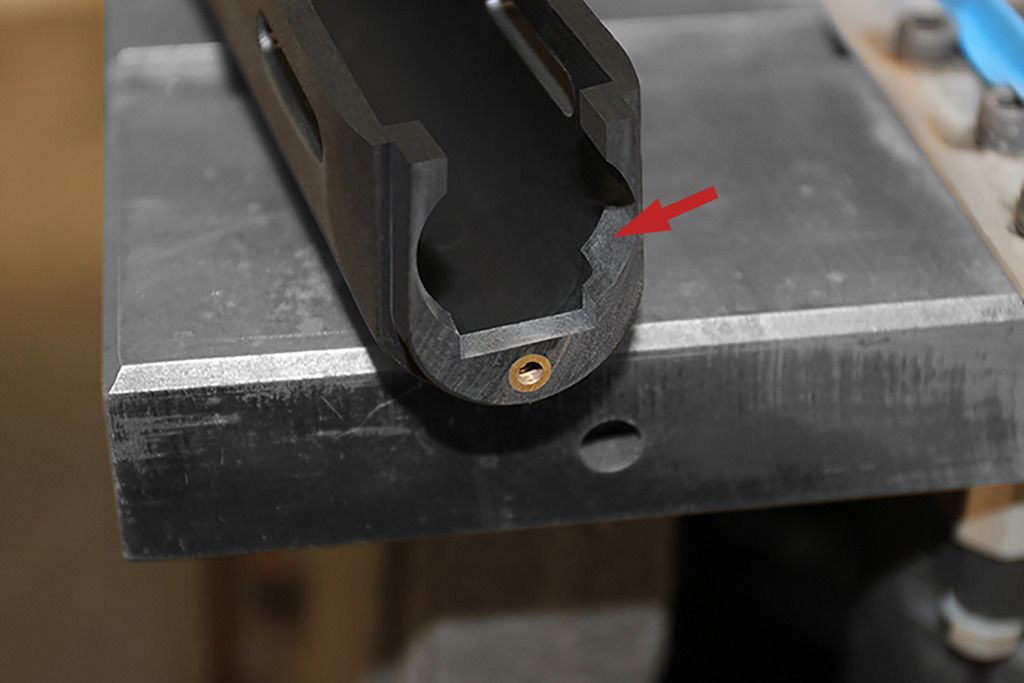
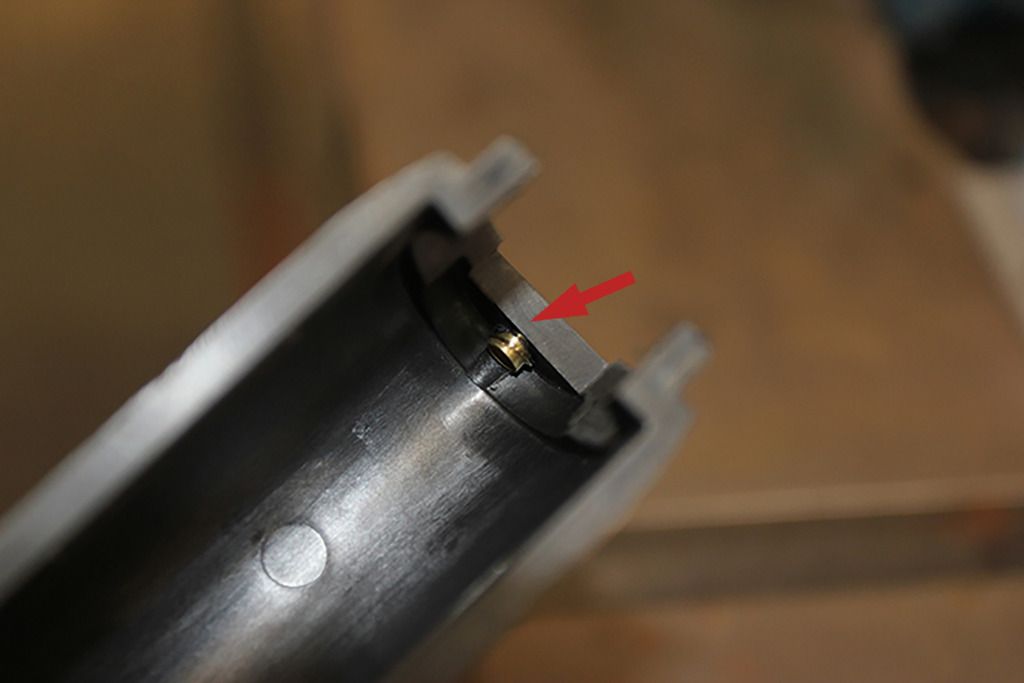
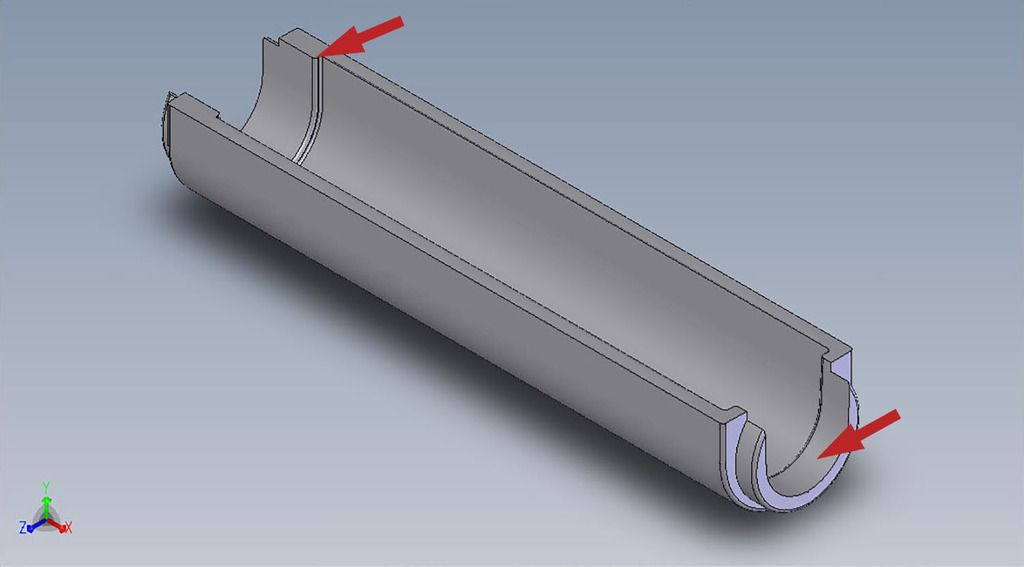
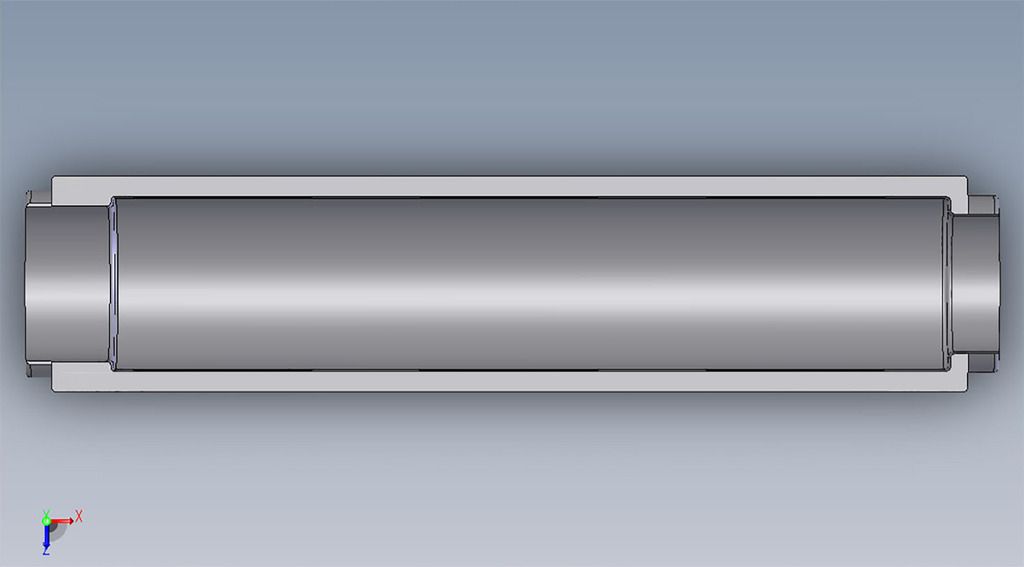
