I popped my first ever composite part out of the mold yesterday and was thrilled with the results. The surface is flawless!
The only problem I'd like to work on for the next part out of the mold is the disruption in the weave around the edges of the soric core. Any way to protect the weave? Add a layer of veil or something between the soric and the surface layers?
Layup was 2 layers of stabilized 200gsm 2x2 twill, soric core (the rectangular cutouts were in case I had to really pull hard to get this thing out of the mold, turns out I didn't at all), then two more layers of carbon. After that was peel ply, flow media, vac bag. I used the MTI hose and MTI valves and I think based on the surface finish on both sides I have the resin part pretty nailed?
2 layers carbon + soric, 2 more layers of carbon after this. Cutouts were to add shear strength in case I had to really yank to get it out of the mold.

Infusion happening.

Here's the soric edge print through on the face of the part that I'm wanting to eliminate. The surface is perfect, just a shift in the weave that you can see.

One more angle of the issue:

Backside looks great to me but, again, not a lot of experience to go on here.
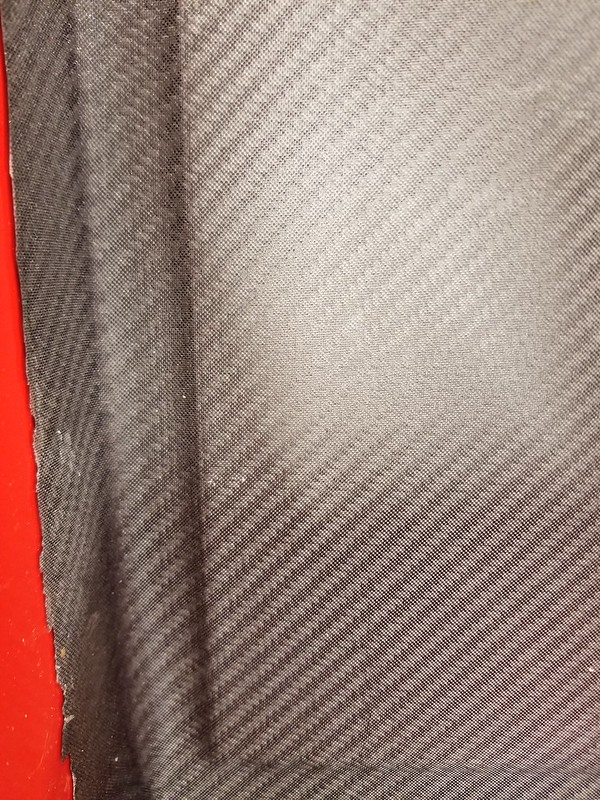
Couldn't be happier in the end for my first part, just always looking to improve!
Step one in my mind is to eliminate the cutouts in the core but there will still be the issue at the edge of the core, I don't want to wrap the core up the corners.
Thanks,
Alex