Thanks to Matt and Paul for the idea, and after a fair bit of research, I found the solution to my surface finishing issue from my pressure bagging experiments/
Gentlemen (and any lady lurkers) , Let me introduce "Thermal compression moulding". Its not a panacea to all moulding ills, and it takes some special kit somewon't have, but here we go.
The method relies on the high thermal expansion of silicone rubber to provide high mould forces, without a messing with bags. You can get very clever and use multiple blocks of silicone to pressure really nasty bits of CF.
Method.
1.) Wax up your tool - use sheet wax.
2.) FILL the mould ALMOST completely with silicone rubber (condensation cure: around 2 litres here)
My mould is CNC milled aluminium

3.) Remove cast plug after 24 hours.

4.) Layup mould: this is VERY tricky. We put two finish layers in each half of the tool, and struck them off with a knife. Then we wrapped two pieces of bulk CF prepreg around the silicone.
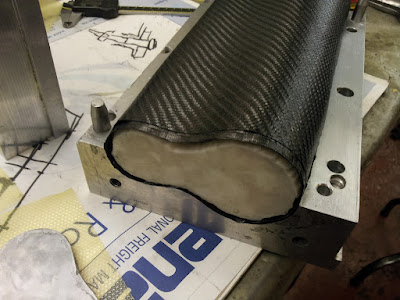
5.) Assemble metal tool, put in silicone.
6.) Whack up 6 M12 screws to lock the halves together.
7.) Put in an oven 80 deg C, 8 hours.
8.) Demould tool !
9.) PERFECT result.
(removing the silicone IS a bitch)
Wrinkles to the technique:
1) load the silicone with 30% carbon black to increase the thermal conductivity.
2.) Mould around a tapered aluminium core that can be extracted after moulding to allow the silicone to be removed easier......
3.) Experiment, by embedding a thermocouple in the plug, and find out the time constant of your plug: Tailor the temperature profile to ensure maximum expansion of your core when the pre-preg reaches your cure temperature. Remember that the rubber is not terribly thermally conductive.
4.) Leave space in one end as a dead volume that can be used to control mould pressure, by filling the volume with thin metal plates.
Pictures when I have 'em.