BlackNDecker
|
|
Group: Forum Members
Posts: 92,
Visits: 251
|
Greetings all, I bought a brand new OEM steel roof and plan to make a mold and eventually a carbon fiber roof. A little background...My car is a 2007 Honda Civic Si and comes with a heavy sun roof assembly (this comes standard from the factory). I contemplated simply swapping roofs for the OEM "non-sunroof" steel roof. That would save me around 20 lbs...but instead of going that direction I've decided to make a carbon fiber roof and hopefully save 30+ lbs. Some pictures of my progress... Made some progress on the roof project. Transferred it out to the garage: 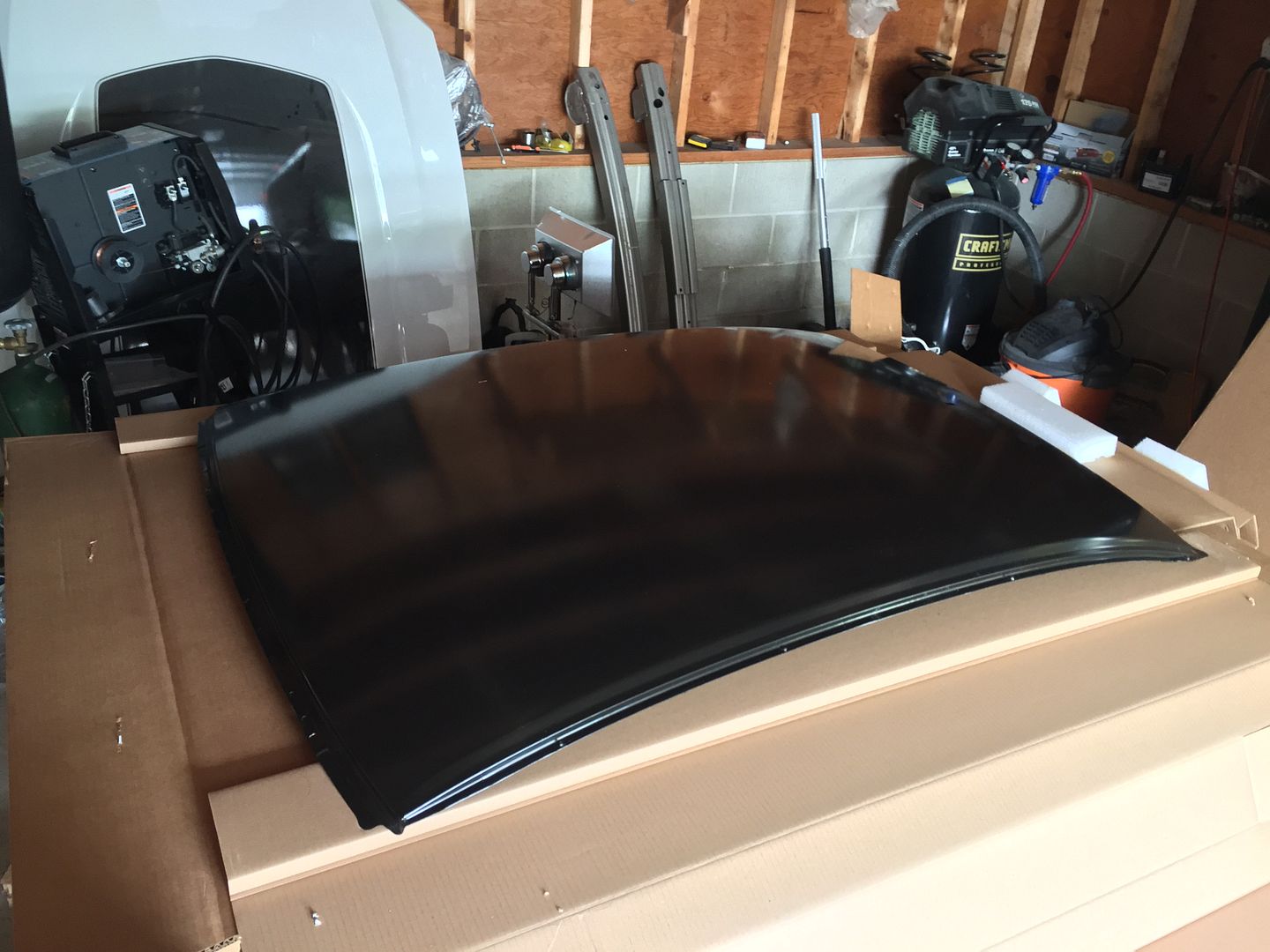 The antenna hole will be covered: 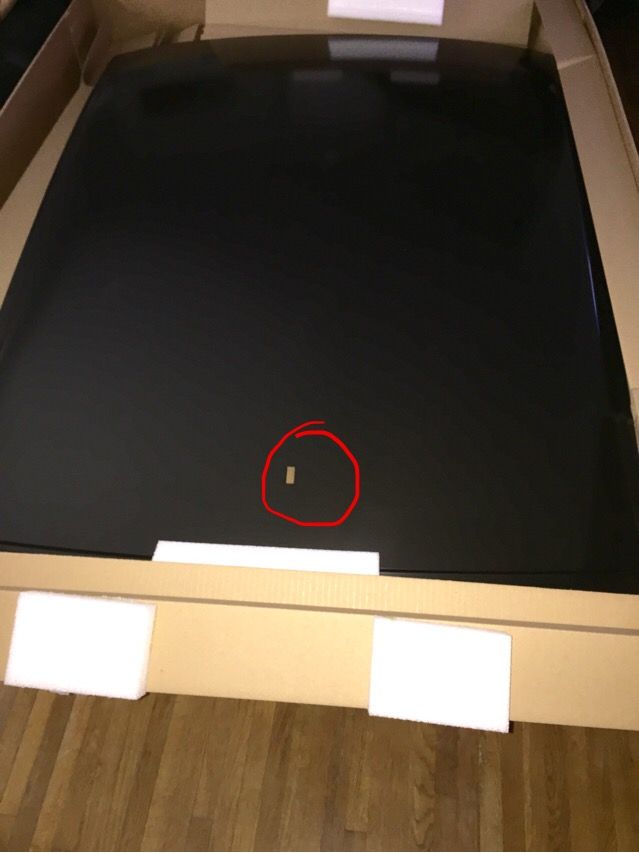 And the tabs for the weather seal have to be cut off: 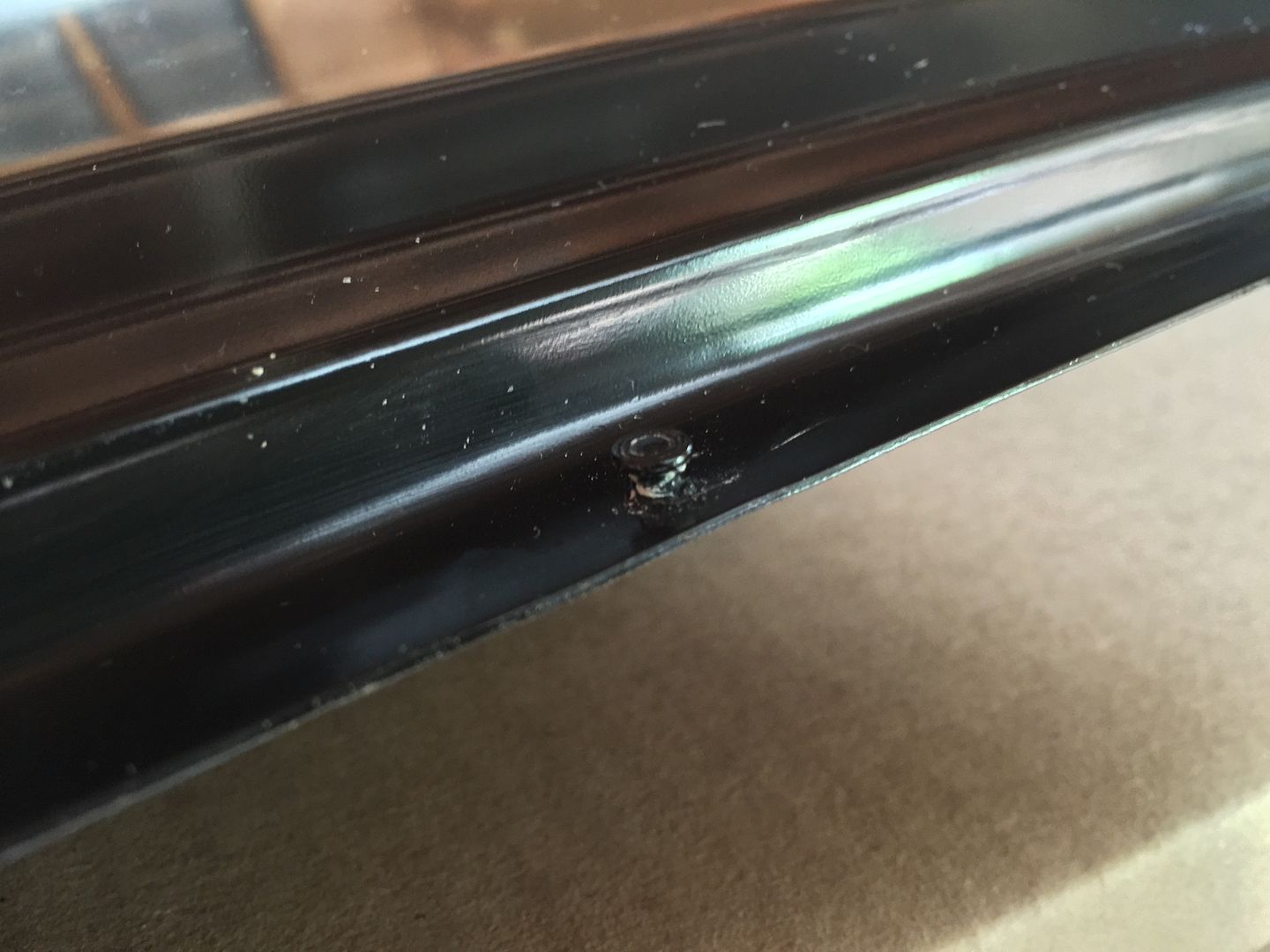 Luckily I have a Dremel for these types of projects: 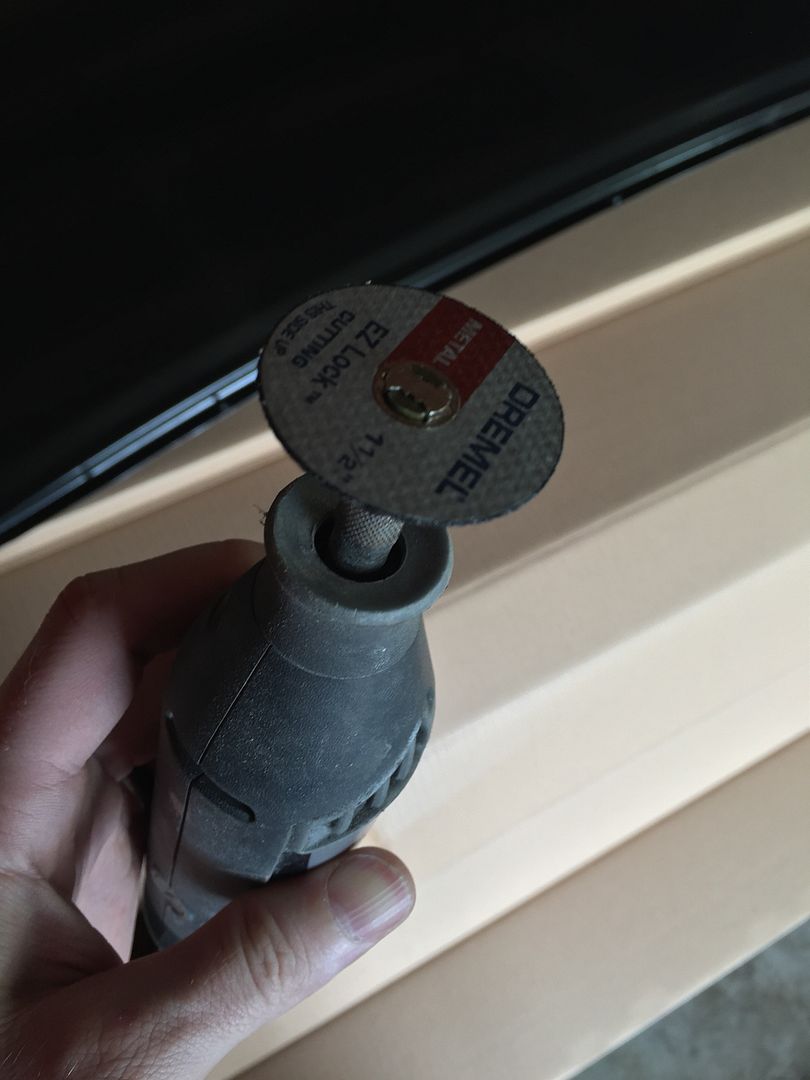 Made some flanges: 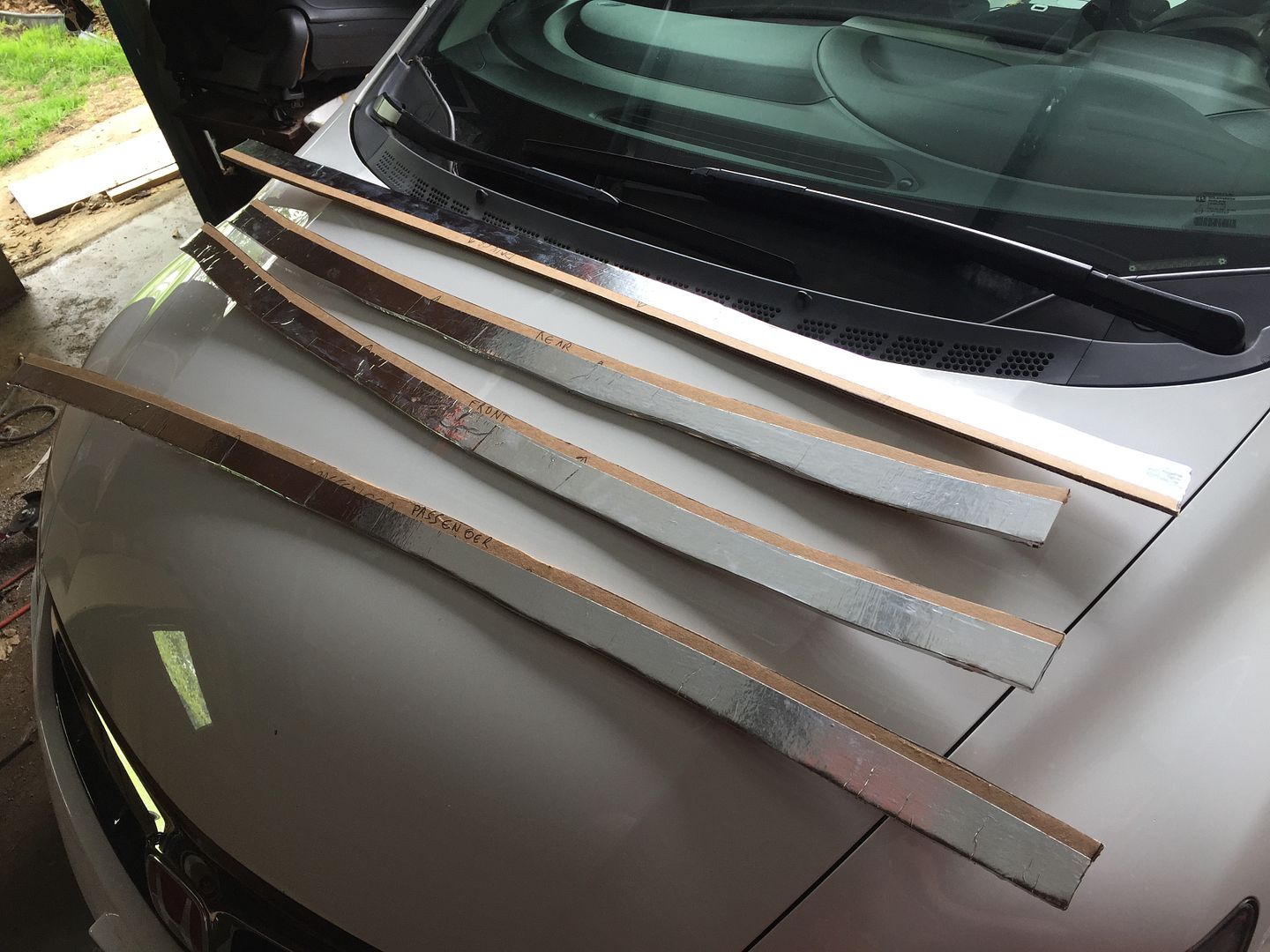 Antenna hole covered (with a fresh coat of wax): 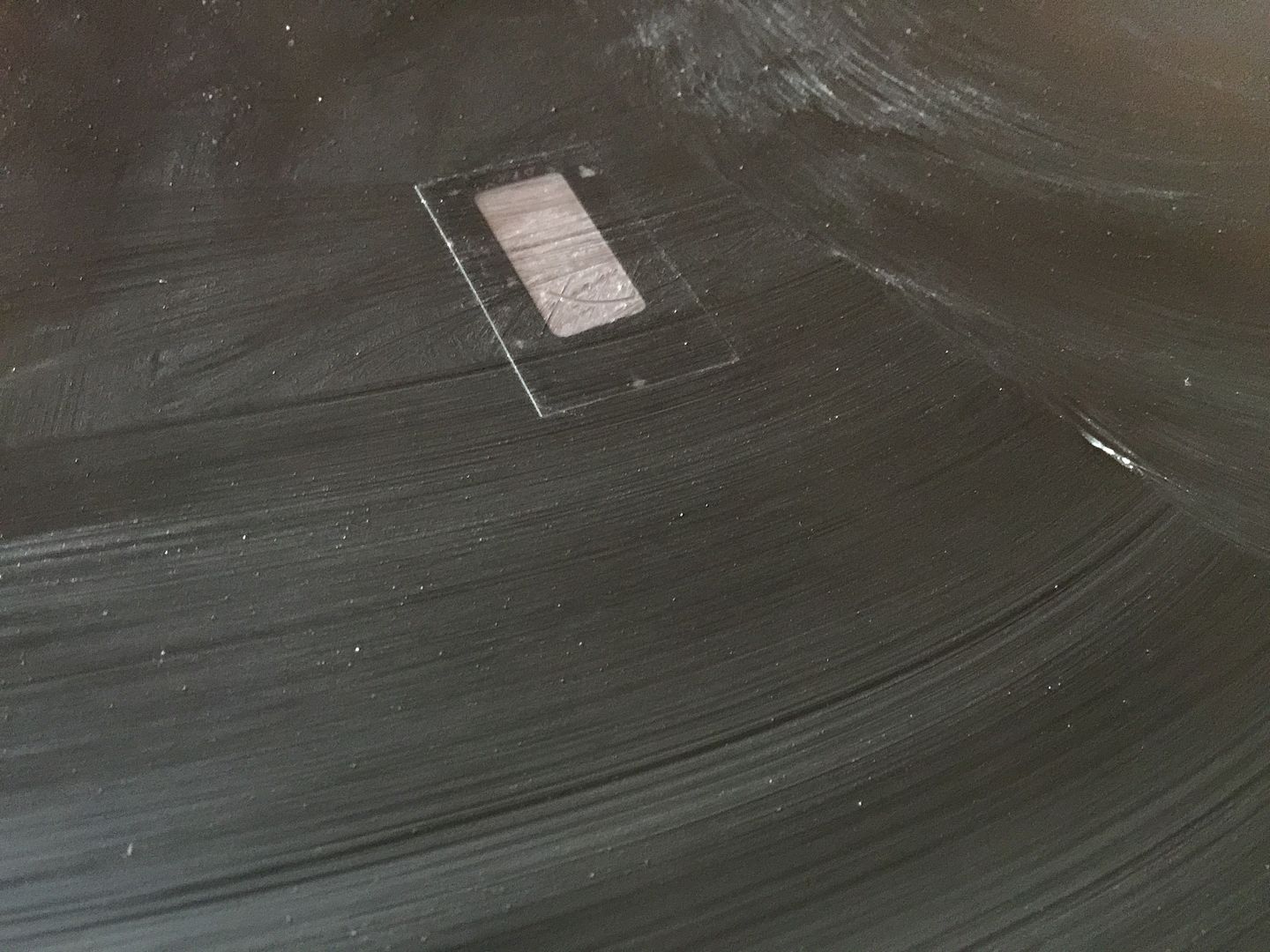 Flanged, waxed, and ready to go... 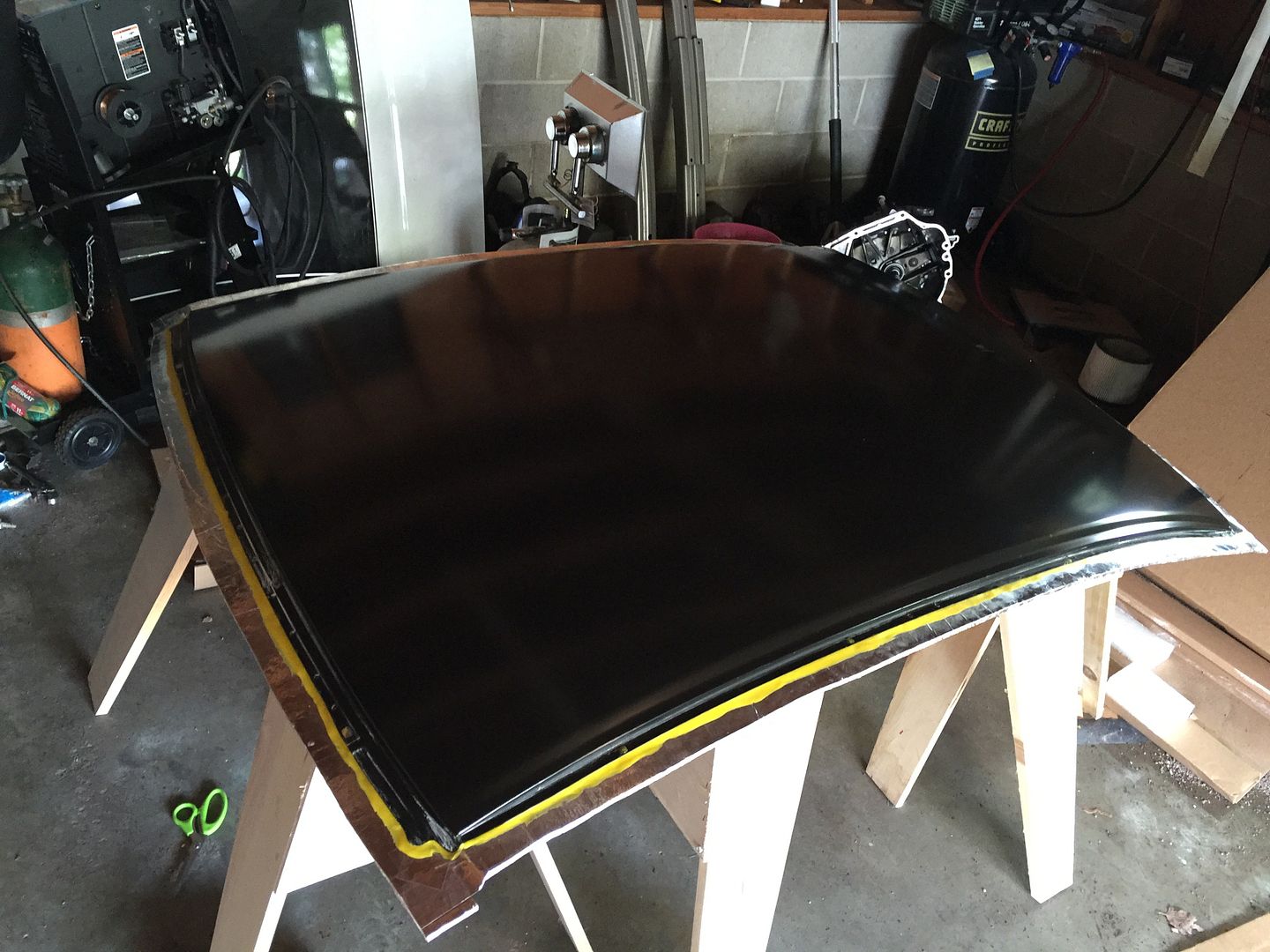 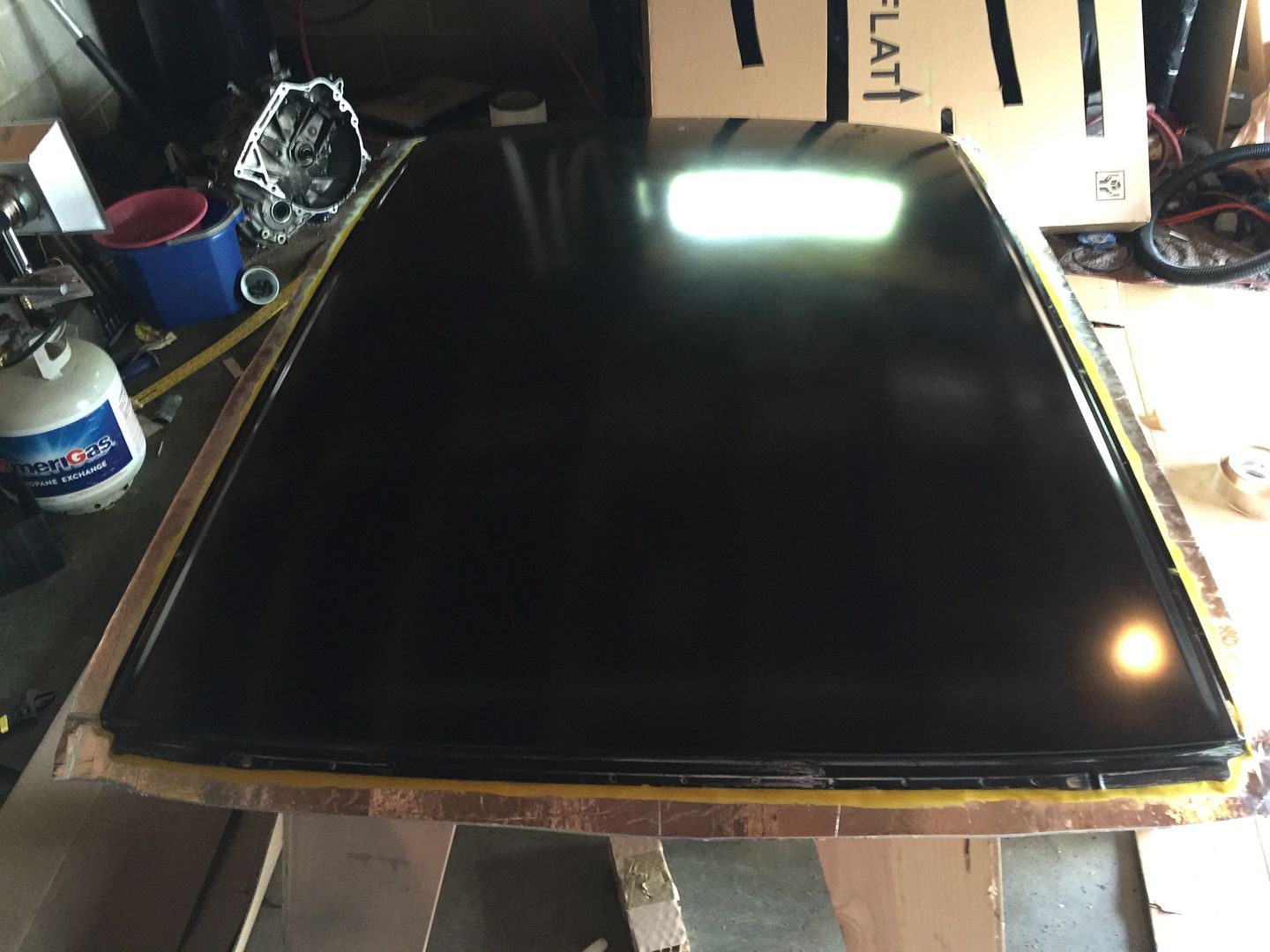 Unfortunately, it's going to be too humid all weekend to lay the gel coat...so I'll probably have to wait until Monday or Tuesday. fml
|
|
|
BlackNDecker
|
|
Group: Forum Members
Posts: 92,
Visits: 251
|
I decided to go ahead and lay down some gel coat this afternoon. It is really hard to get everything covered in one go due to the large surface area...but I was able to get it relatively even. It's a little thin and I will have to reinforce it with another layer of gel coat tomorrow.
|
|
|
Hanaldo
|
|
Group: Forum Members
Posts: 2.5K,
Visits: 28K
|
Really narrow flanges, will you be infusing?
|
|
|
BlackNDecker
|
|
Group: Forum Members
Posts: 92,
Visits: 251
|
Yes and yes. The flanges are pretty narrow...about 2.5". I'm a little nervous about brushing on a second coat of gel coat. The base coat is really thin in some areas and will need a second coat. Any pointers or helpful advice before the second coat?
|
|
|
Hanaldo
|
|
Group: Forum Members
Posts: 2.5K,
Visits: 28K
|
Yeh it's a harrowing time haha. What temperature is it where you are working and what did you catalyse the first layer of gelcoat at?
|
|
|
BlackNDecker
|
|
Group: Forum Members
Posts: 92,
Visits: 251
|
I catalyzed at exactly 1.5%... Tomorrow looks like this:
|
|
|
Hanaldo
|
|
Group: Forum Members
Posts: 2.5K,
Visits: 28K
|
Hmmm, could be an issue. I would be using 2% catalyst at 25 degrees and INCREASING that level for any decrease in temperature... For 23 degrees you probably don't need to change too much, 0.5% if anything. With the tests I've done with my tooling system, I go up 1% for every 5 degrees drop in temperature. Mix up smaller batches if you need more time to apply it to the pattern. That said, how long has it been curing now? You might be ok, the unimould system doesn't seem to be very prone to alligatoring. Is the surface tacky at all? If the thinner patches seem tackier than the thicker areas, I would give it a bit more time, maybe even apply some heat. Then give it a quick wipe over with acetone to restore some tack.
|
|
|
BlackNDecker
|
|
Group: Forum Members
Posts: 92,
Visits: 251
|
Thanks for the back and forth. Sometimes it's just nice to talk through the stress of mold making. I've had some pretty epic (read expensive) failures.
|
|
|
Hanaldo
|
|
Group: Forum Members
Posts: 2.5K,
Visits: 28K
|
Yeh so have I! Don't think you can play the game without having a few losses... For what it's worth, I suggest doing a test with your stuff. With tooling gelcoat, you want to have a pot life of about 20 minutes. You can extend that a little bit if you have to, but I find it related directly to how long you need to leave it to cure. With a 20 minute pot life, you should find that it cures to a stage where you can move to the next stage in 4-6 hours. With 25 minutes, that becomes more like 6-8 hours, so it makes a big difference. Therefore I suggest doing a couple of test batches so you can work out exactly how much catalyst you need at any given temperature, and then always aim for your 20 minute pot life if you can, mixing smaller batches for larger projects if need be. The way I worked it out is I measured out 4 batches of 25ml of gelcoat. Measure the ambient temperature of where you are working so you know what you're going off, and then catalyse one batch at 1% one at 2% one at 3% and one at 4%. The one at 2% is your control, because you know that the ideal mixture is 2% at 25 degrees. Use different mixing sticks for each one so you don't contaminate the subsequent batches. Set a stopwatch going then set an alarm every 5 minutes for roughly half an hour, and come and check on your test. Alternatively you can just stand and watch, but that's quite literally like watching paint dry... Have a play with each one at every 5 minute interval, swirl them around and poke them with the mixing stick to see how the viscosity changes and eventually they start to gel. The 4% one will start to gel first, so take note of how much time has passed on the stop watch. Do the same for each one until your 2% control goes. You should notice that your 3% batch will take roughly double the time your 4% batch took, 2% will take double the 3% batch etc. Depends on your system and how old the chemicals are etc. but that's about right. From those results you can work out exactly what catalyst level you need for the ambient temperature, and you can be confident that it will have cured correctly when you move onto the next stage.
|
|
|
BlackNDecker
|
|
Group: Forum Members
Posts: 92,
Visits: 251
|
That is a really good tip...but in addition to varying temperature, we have widely varying humidity from day to day. It just seems like too many variables to try and account for with an outdoor shop  Got an early start this morning. The prior gel coat layer behaved itself and I brushed on another reinforcement coat.
|
|
|