ihave2seats
|
|
Group: Forum Members
Posts: 5,
Visits: 20
|
Hey, I'm new here but have always loved cars. This project will be for an Audi S4. For our car platform however, the intake options are less than ideal - otherwise I would buy one. An expensive but poor design:  This intake design is ideal, but it isn't for our car and serves as the inspiration for the project:  That said, my idea is to construct a snorkel that could work in conjunction with one of the heat shield only designs as such below: 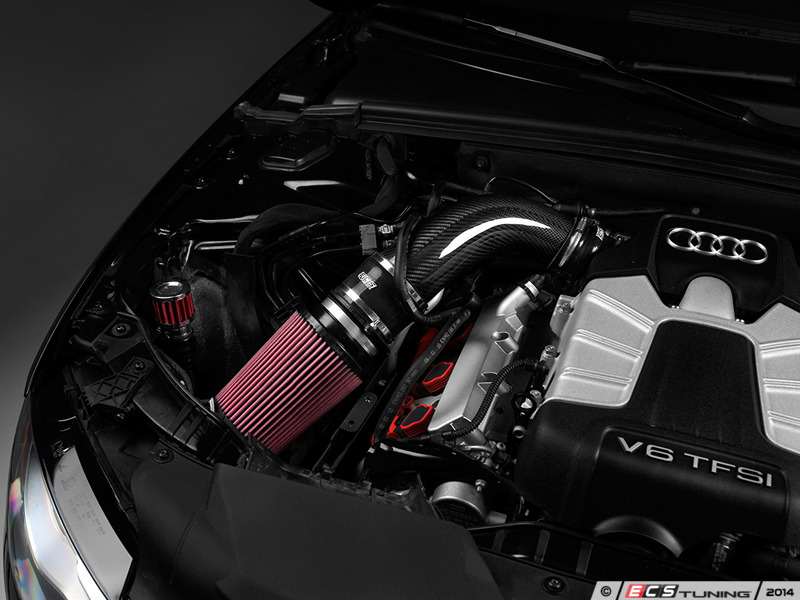  Now, while I have never done any projects like this - I am pretty handy and learn quickly. I am looking to make a permanent mould, so that it can be replicated... but I have to design the shape first. I'm sure more questions will arise, but the two that I can think of are: 1. What is the best method to create an accurate mould? 2. If I make it a two piece that surrounds the filter, how do I set the threads for the screws to bolt down the lid? (See below for example): 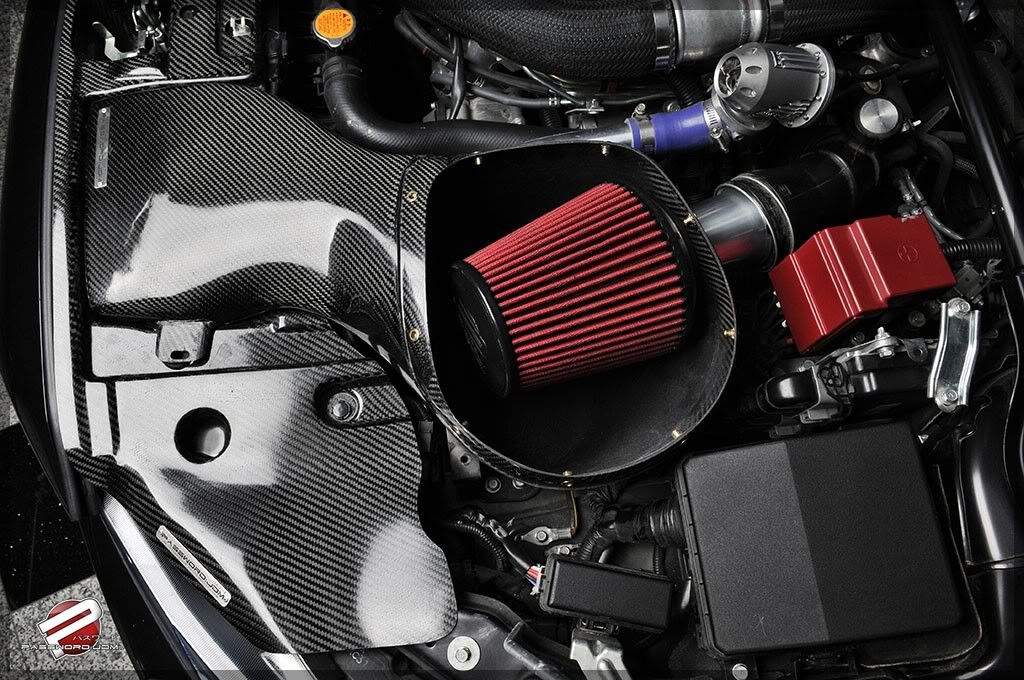 Thank you SO MUCH in advance!!!
|
|
|
Hanaldo
|
|
Group: Forum Members
Posts: 2.5K,
Visits: 28K
|
The methods outlined in Easy Composites tutorial videos are really the most straight forward way to tackle a job like this, so I'd suggest starting there. The pattern making tutorial is very relevant, and then the split mould tutorial is likely to cover the techniques and materials for making the mould. Not sure if you have ant CAD experience, but if not then getting someone to fab something up out of metal may be the quickest and most accurate to tackle the pattern.
As for the fixings, there's a few options really, BigHead fasteners, nutserts, nut plates, etc etc. Depends on your design and what will work.
|
|
|
ihave2seats
|
|
Group: Forum Members
Posts: 5,
Visits: 20
|
+xThe methods outlined in Easy Composites tutorial videos are really the most straight forward way to tackle a job like this, so I'd suggest starting there. The pattern making tutorial is very relevant, and then the split mould tutorial is likely to cover the techniques and materials for making the mould. Not sure if you have ant CAD experience, but if not then getting someone to fab something up out of metal may be the quickest and most accurate to tackle the pattern. As for the fixings, there's a few options really, BigHead fasteners, nutserts, nut plates, etc etc. Depends on your design and what will work. Yes, that is where I first started - watching the videos. It is what led me here to the forum (which I'm really happy about as having a resource like you guys really gives me much more confidence!). Thanks for pointing out the fastener options. My design will most likely replicate the last picture - which are those closest to do you believe? Also, a concern will be heat resistance. Is there anything I am able to layer into the CF that will aid with this? I think for me, the hardest part is going to be creating the lid section precisely (which to you might sound super easy)
|
|
|
Hanaldo
|
|
Group: Forum Members
Posts: 2.5K,
Visits: 28K
|
It's sort of a bit grainy to tell, but they look like nutserts to me.
Heat resistance is all down to the resin you're using. If you're planning on wet laying these, there's quite a few high temperature resins that will handle 160+C with a post cure. If you want to infuse you may struggle to find anything higher than 95-100, especially if you arent wanting to buy in bulk. Both wet lay and infusion will require a post cure up to the planned operating temperature in order to realise those temperature capabilities, so you would need a solution for getting them to that temperature for a few hours. Otherwise, if you have the facilities, pre-pregs will do about 120.
|
|
|
ihave2seats
|
|
Group: Forum Members
Posts: 5,
Visits: 20
|
+xIt's sort of a bit grainy to tell, but they look like nutserts to me. Heat resistance is all down to the resin you're using. If you're planning on wet laying these, there's quite a few high temperature resins that will handle 160+C with a post cure. If you want to infuse you may struggle to find anything higher than 95-100, especially if you arent wanting to buy in bulk. Both wet lay and infusion will require a post cure up to the planned operating temperature in order to realise those temperature capabilities, so you would need a solution for getting them to that temperature for a few hours. Otherwise, if you have the facilities, pre-pregs will do about 120. Right, that makes sense. After looking a very hot IAT for this car would be around 87.50°C, so any of those would work. The pre-pregs 120 would be optimal. In addition to this, I would probably use a heat resistant clear coat. This leads me to another question - is there any way I could help reduce the internal temp of the intake by the construction of the CF? I read something about foamcore. Sorry if this is a very simple question, but from the tutorial it looked like you could cure it in a regular oven as long as you ran the vacuum line outside to the pump. I only ask this because you mentioned having the facilities (in my mind that means special equipment! ha) Based on your expertise, aside from the lid, would you see this being a two piece mould?
|
|
|
oekmont
|
|
Group: Forum Members
Posts: 550,
Visits: 27K
|
Yes, a sandwich core will reduce intake temp, because it insulates the inside from the hotter engine bay. But I really don't think this will made a significant performance upgrade, unless you are really going race specs here. This will absolutely be a (at least) two piece mould. Knowing that I will be the fun killer again, I would advice you to put back your idea and start with something far more simple. Even if you are quite a prodigy, you will have trouble with this as a first project. This not only comes down to simple questions like if it needs to be two piece mould, that you can just clarify at a forum, but to get some feel for techniques, materials and processes. Trust me, most of us paid the early ambition price. You will get a steeper learning curve by starting with a one piece mould project, at sorting out problems one at a time (few at a time, to be honest), at save money.
|
|
|
ihave2seats
|
|
Group: Forum Members
Posts: 5,
Visits: 20
|
+xYes, a sandwich core will reduce intake temp, because it insulates the inside from the hotter engine bay. But I really don't think this will made a significant performance upgrade, unless you are really going race specs here. This will absolutely be a (at least) two piece mould. Knowing that I will be the fun killer again, I would advice you to put back your idea and start with something far more simple. Even if you are quite a prodigy, you will have trouble with this as a first project. This not only comes down to simple questions like if it needs to be two piece mould, that you can just clarify at a forum, but to get some feel for techniques, materials and processes. Trust me, most of us paid the early ambition price. You will get a steeper learning curve by starting with a one piece mould project, at sorting out problems one at a time (few at a time, to be honest), at save money. Thanks for your reply! And I would much rather have real advice - even if it puts a damper on ambition. I am just trying to solve a problem with this relatively hot engine bay, that progressively produces more heat with some specific modifications. Many who have had the car longer see this problem and look for any way to help. Provided I make an investment to create this with that goal in mind, I might be able to make them for others. And I totally get your point about the learning curve. That is why I was considering making the intake tube first before doing the airbox. That way it is much more simple (although not a one piece), but would allow me to experience a more simple project first. The only difference is that I would most likely be replicating the intake tube I purchase instead of creating a mould for it. Thoughts on this?
|
|
|
oekmont
|
|
Group: Forum Members
Posts: 550,
Visits: 27K
|
I thought the actual design is far from ideal? So why should replicating it be an option?
Just because there are even trickier parts out there doesn't mean that this is a good beginners project. it seems like you've come to the conclusion, that the airbox might be a bit difficult to start with. As someone who actually reached a point where projects like this are possible, I just wanted to tell you, that I think the intake is already fairly complex. Split mould, compound curved flanges, that are topics that will likely cause you problems, especially if you never done composites before. This videos make it look quite easy, but only looking a video doesn't make you master those techniques. I really doesn't hurt to just start with a simple one piece mould. A cover ore something. Your experience from that will make any further part that much better. And it will likely save you both time and money in the end. To the temperature topic: just making the intake out of carbon will rather increase the temperature of the air, as the tube will be (when made properly) is thinner than the original, and carbon has a higher thermal conduction coefficient than the original material.
|
|
|
Steve Broad
|
|
Group: Forum Members
Posts: 408,
Visits: 4.1K
|
Sod, it, just go for it :-) What's the worst that can happen? You waste material and money but learn lots. If you have had any experience with woven fibre glass mat then CF isn't a lot different to deal with. The main differences are the far longer curing times and much more expensive materials. With regard to the fabrication of an induction system, I am in the process of designing and making one for my project car. I paint all my carbon so I am not looking for a shiny finish, which makes preparing the moulds simpler :-)   I am using plastic ducting joints and tubes to make the pattern out of, designing the system on the car so no CAD involved :-) Once I have the shape as I want it a split mould is made from the patterns using high temp resins as I will be using prepreg. Once I had the basic shape I filled it with expanding foam to strengthen it then smoothed it out with filler. The sharp internal corners/edges will be filleted on the mould.   The moulds will be of the split variety. For small items I use a second hand electric oven sourced from eBay with a hole drilled for the vacuum tube. I used 3D CAD to design the filter box, but there was no real need as it is pretty simple. ITG will be making a filter to suit. This service is worth considering if you have space constraints.      Filter box is made from two layers of 210gm/m2 pregreg and weighs 251gms but will be a little heavier once I have tidied it up and painted it :-). I will make the ducting with three layers as this needs to be a little more robust and has to be able to resist partial a vacuum (hopefully the system wil be good enough to supply all the air the engine requires without too much of a pressure drop).
|
|
|
ihave2seats
|
|
Group: Forum Members
Posts: 5,
Visits: 20
|
+xI thought the actual design is far from ideal? So why should replicating it be an option? Just because there are even trickier parts out there doesn't mean that this is a good beginners project. it seems like you've come to the conclusion, that the airbox might be a bit difficult to start with. As someone who actually reached a point where projects like this are possible, I just wanted to tell you, that I think the intake is already fairly complex. Split mould, compound curved flanges, that are topics that will likely cause you problems, especially if you never done composites before. This videos make it look quite easy, but only looking a video doesn't make you master those techniques. I really doesn't hurt to just start with a simple one piece mould. A cover ore something. Your experience from that will make any further part that much better. And it will likely save you both time and money in the end. To the temperature topic: just making the intake out of carbon will rather increase the temperature of the air, as the tube will be (when made properly) is thinner than the original, and carbon has a higher thermal conduction coefficient than the original material. The inlet tube isn't an issue, its the open air filter design that I see as not ideal. I believe that I could lay the material fairly easily and successfully, I would just be concerned with making the initial mould shape (I'm fairly sure I could construct the mould effectively once I have the template). Regarding temperature, I am trying to find a solution for that as I know that carbon fiber isn't exactly the best in that regard. +xSod, it, just go for it :-) What's the worst that can happen? You waste material and money but learn lots. If you have had any experience with woven fibre glass mat then CF isn't a lot different to deal with. The main differences are the far longer curing times and much more expensive materials. With regard to the fabrication of an induction system, I am in the process of designing and making one for my project car. I paint all my carbon so I am not looking for a shiny finish, which makes preparing the moulds simpler :-)   I am using plastic ducting joints and tubes to make the pattern out of, designing the system on the car so no CAD involved :-) Once I have the shape as I want it a split mould is made from the patterns using high temp resins as I will be using prepreg. Once I had the basic shape I filled it with expanding foam to strengthen it then smoothed it out with filler. The sharp internal corners/edges will be filleted on the mould.   The moulds will be of the split variety. For small items I use a second hand electric oven sourced from eBay with a hole drilled for the vacuum tube. I used 3D CAD to design the filter box, but there was no real need as it is pretty simple. ITG will be making a filter to suit. This service is worth considering if you have space constraints.      Filter box is made from two layers of 210gm/m2 pregreg and weighs 251gms but will be a little heavier once I have tidied it up and painted it :-). I will make the ducting with three layers as this needs to be a little more robust and has to be able to resist partial a vacuum (hopefully the system wil be good enough to supply all the air the engine requires without too much of a pressure drop). Steve, thanks for taking the time to post your project! It looks super nice! I assume you're doing a V mount setup? It looks awesome! I hope to see your pictures of the inlet mould/result prior to paint! I really like the way you used the plastic to essentially piece together the mould and then refine it with the filler.
|
|
|