By Ragged99 - 1/2/2014 10:12:18 PM
Hi Guys,
I thought I'd pop up and show you what my mate Tim and I are doing with the Easy Composites systems in our garages. We're what Enzo Ferrari called "Garagistas" in that we both own AB Performance Sabre race cars, and we build, modify, and prepare them to run in a race series called RGB with the 750 motor Club. In short we're clubman racers and we like building stuff. Our cars are powered by bike engines, and we aren't allowed wings. so we need to generate aero efficiency from the main body of the car. Tim is in mid build of his new Sabre and wanted non standard bodywork to try and improve the aero efficiency, and I wanted different bodywork on my year old Sabre as the car is currently too big to fit in my garage without partially disassembling it, which is a right pain when you arrive home at midnight after a weekends racing. Also I'm a big lad and ultra lightweight carbon bodywork will help me get down to the minimum weight limit for the car and driver. So we basically decided to build our own bodywork from scratch. I'd done some small scale fibreglass, buck and mould building in the past on a former car, and we were pretty impressed with the resin infusion process so decided to give the Easy Composites system a try. We even ran a test infusion process on my glass coffee table top ;-) to make some flat carbon panels. Although we've never tackled anything of this size, we're doing the full spectrum of build a buck, surface it, then make a mould, them carbon resin infused parts. So for the last couple of months we've been building a buck around Tim's partially complete chassis. Well in fact Tim has 90% of the work and I'm chipping in at weekends. The buck has been built from timber, 3mm mdf board which is nicely flexible for simple curves, filler and foam. and we're now at the pattern coat primer stage. We've learned a lot along the way, but basically we've followed the video tutorials and have just scaled up the processes. Full details are on Tim's website at www.hoverd.orgDetails of my racing are at www.rgbracer.com.. and the main AB performance website is www.abperformance.co.uk. But to whet your appetite here's a picture of the buck in pattern coat. 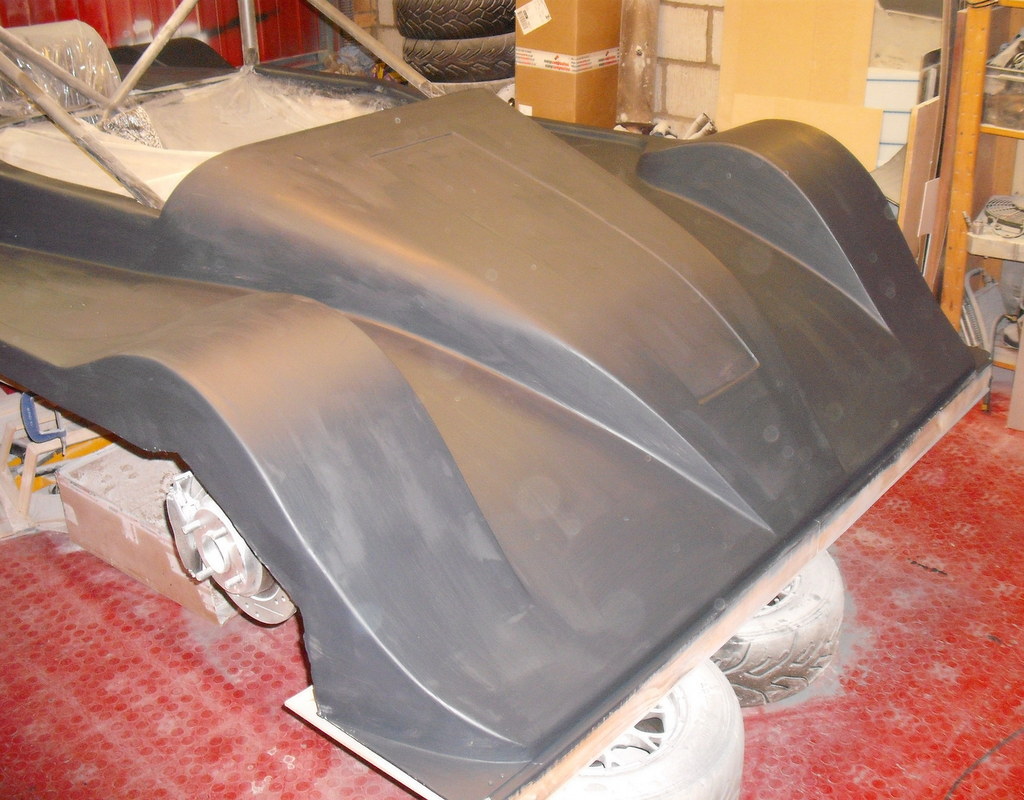 Cost to date in materials for the buck, pattern coat, foam etc is about 500 quid, although I've just spent about 600-800 on Unimould materials + CSM for the mould making stage. |
By andygtt - 4/15/2014 1:40:14 PM
this is loosely how i do the return edges on my parts... if the areas are hard to get to when the mould is assembled i will often lay it into the mould section carefully and trim it right to the edge, then assemble and overlay the other side around 10mm... then if you do happen to have a void (it happens to me occasionally) then the resin still flows to the carbon edge and often fills the void and you end up with a slightly heavier part but the right shape.... much better than having a bridge that you then have to fill.
great job so far, very impressive
Ragged99 (15/04/2014)
Then when laying up the mould, tack the carbon down into the top moulds without the base plate in place. and trim back to edge with a couple of inches over lap, and if necessary snip the overhang edges to allow them to fold easily along the return Before fitting the baseboard , tack some carbon tape in place for the internal flange. Then fit the board and carefully lay the carbon in place from the other half in place. Then stack and envelope vac bag it in the normal way. This seems a reasonable plan, but it is a fair bit of a faffing around to get a return edge, .... am I approaching this correctly? Adrian
y) then the resin still flows to the carbon edge and often fills the void and you end up with a slightly heavier part but the right shape.... much better than having a bridge that you then have to fill. great job so far, very impressive
|
|